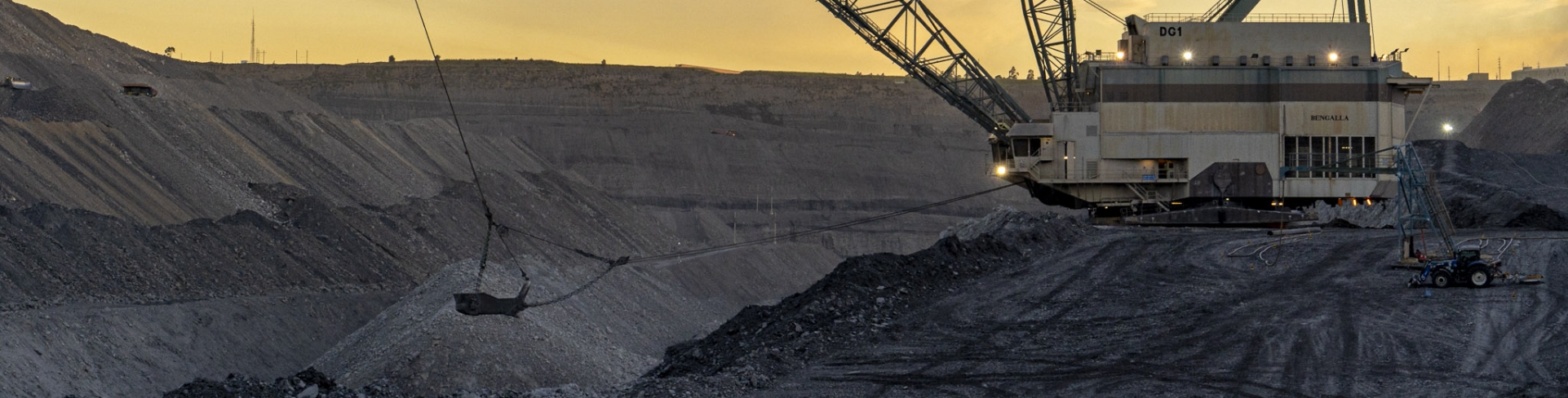
Bindaree Beef High Voltage Upgrade
Bindaree Beef High Voltage Upgrade
Background
Bindaree Beef had 6 x oil filled 22kV/0.433kV transformers installed ranging in size from 500kVA to 1,100kVA some of which were over 40 years old. Most had inadequate access, bunding and fire prevention measures in relation to modern standards. The site transformers were also not evenly loaded with one smaller transformer struggling with heavy loads and others lightly loaded.
PCE were requested to develop a replacement strategy for the transformers that would provide the site with a stable and compliant transformer network. This project subsequently developed into also designing replacement 433V main switchboards and cabling for the new transformers as the site’s original main switchboards were also non-compliant with modern standards which aim to protect personnel from injury due to contact with exposed live conductors, fault currents and arc flash.
Site Design Restrictions
A combination of 3 x new 1500kVA transformers and 433V switchboards would suit site load requirements and allow even loading across the transformers. But as with most existing industry sites, the problem would be where to install these extra transformers while the existing transformers remain in service? Proximity of the new transformers and switchboards was a major consideration given the limited spare real estate availability.
AS2067:2016 states that transformers (free standing or kiosk type) must be installed in a way that minimizes risk to people, environment and other plant in the event of a transformer major failure (fire/explosion/etc.). Table 6.1 ‘Clearances for Outdoor Transformers’ states the minimum distances required to other transformers, buildings, combustible surfaces etc. The larger the transformer the greater the clearances required, for a 1500kVa transformer that would hold over 1000ltrs of oil, 3 meters and 7.5 meters is required to other transformers and combustible surfaces. In contrast, if a ‘Dry Type’ transformer is installed, 1.5mtrs is acceptable for both regardless of the size of the transformer.
Agreed Design
Due to limited available space, and risk of fire and oil spill concerns it was agreed to fit 3 x new cast resin core dry transformers on an elevated open platform over a surplus area close to the major site loads. These transformers were supplied by TMC Melbourne and are made in Melbourne, Australia. As with oil transformers these air transformers can be fan cooled to give additional capacity if required, it was decided therefore to add cooling fans that could be used to gain an extra 300kVA if required in the future.
Dry Transformers – General Characteristics
These are generally divided into two types:
- VPI HV/LV coils (vacuum impregnated coil in open air) on laminated core
- Cast resin coils (coils fully encapsulated in resin) on a laminated core
The fully encapsulated cast resin core design gives reliability and longevity advantages of the open VPI design, therefore most modern dry transformers supplied are cast resin.
Some advantages of modern cast resin dry transformers
- No oil, so no bunding is required (cost saving)
- Low fire risk (self-extinguishing)
- Closer installation possible with areas of limited real estate (reduces costs)
- Open design meaning ease of inspection or repairs when required
- Long life, highly reliable and low maintenance requirements (no oil sampling or filtering)
- Negligible HV partial discharge risks due to encapsulated windings
- Suitable for harsh, dusty and humid environments
- Suitable for indoor or outdoor installation
Figure 1 - Example of a dry resin transformer core
Figure 2 - Example of a dry resin core transformer complete with outgoing LV air circuit breaker
Disadvantages of cast resin dry transformers
The initial cost of modern cast resin transformers compared to an oil transformer will in most cases be a little higher. This is easily offset by the reduced design and installation costs of bunding (excluding self-bunded kiosks), fire detection/extinguishing systems, ability to be installed in close proximity to other equipment, plus reduced exposure risk to personnel in the event of a major transformer failure.
Dry type transformers can also have higher ‘no-load’ losses resulting in higher power cost at low loads, if this is seen as a problem it can be overcome by the option of a high efficiency design with features such as copper windings (rather than aluminum).
Summary
Design and manufacturing quality of modern resin core dry transformers make them in many cases the ideal choice for new and retrofit transformer applications. PCE are proud to have provided the design, protection and installation plans for the transformer and main switchboards upgrade, resulting in a safe, reliable and compliant site power system.